Pipes are used all over the world for transporting fluids in many settings, for example in the petrochemical, water and energy industries. Leakage from such pipes is of major concern due to the potential social, environmental and economic consequences.
As such, it is important not only to be able to detect leaks once they have occurred, but also to identify cracks and defects early on so that failures can be avoided. An important prerequisite to any of this is being able to identify the exact location of the pipe of interest.
Acoustic techniques can be extremely valuable in all of these areas. They are frequently used for detecting leaks, particularly in the water industry, where such methods have been effective and in common use over the past 30 years.
More recently these acoustic techniques have been adopted to locate underground pipes and characterize defects such as cracks, blockages and corrosion that may cause pipeline failure. Understanding the acoustic characteristics of the dominant wave types which occur in pipes is vital to the success of any of these methods.
Much previous research has shown that the axisymmetric (n=0) fluid-borne (s=1) wave is often the main carrier of the vibrational energy in buried fluid-filled pipes. Researchers from the Institute of Acoustics of the Chinese Academy of Sciences have developed an analytical model to predict the low-frequency dispersion characteristics of the n=0, s=1 wave in a buried fluid-filled pipe.
This research expands on previous investigations on a cylindrical shell filled with fluid, using the Donnell-Mushtari shell theory as a basis along with the assumption that the s=1 wavenumber is much larger than the shell compressional wavenumber. The effect of soil loading on the pipe response is characterized by introducing a soil loading matrix and the s=1 wavenumber has been derived with the frictional stress at the pipe-soil interface included.
Numerical results have shown that the fluid loading is the dominant factor in the prediction of the propagation wavespeed. In particular, for light fluid loading, as is the case for metal pipes, the effect of soil loading can be neglected and the wave can be considered to be non-dispersive at low frequencies. And for plastic pipes, the fluid loading is heavy and simply neglecting the effect of soil loading can lead to a slight underestimation in the calculation of the wavespeed.
For both metal and plastic pipes, the soil loading adds damping to the coupled system, with the increase being more significant for perfect bonding at the pipe-soil interface, compared with the imperfect bonding. This effect increases with frequency and hence increases the wave attenuation more significantly at higher frequencies.
The present theory has been applied to wavenumber measurements made on a buried MDPE water pipe as shown in Fig. 1.
It has been found from Fig. 2 that although the wavespeed is not significantly affected by the inclusion of the frictional stress in the modelling, the wave attenuation increases markedly when the frictional stress is taken into account at the pipe-soil interface. The degree of agreement between prediction and experiment makes clear that the frictional stress need to be properly accounted for in the attenuation predictions.
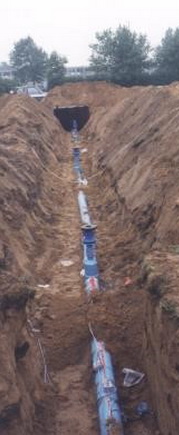
Fig. 1. The test rig under construction (Image by GAO Yan et al.)

Fig. 2. Comparison of measured and predicted wavenumbers: (a) real part; (b) attenuation (dB/m) (Image by GAO Yan et al.)
Reference:
GAO Yan, SUI Fusheng, Jennifer M. Muggleton, YANG Jun. Simplified Dispersion Relationships for Fluid-dominated Axisymmetric Wave Motion in Buried Fluid-Filled Pipes. Journal of Sound and Vibration (Vol. 375, August 2016, pp.386-402). DOI: 10.1016/j.jsv.2016.04.012
Contact:
GAO Yan
Key Laboratory of Noise and Vibration Research, Institute of Acoustics, Chinese Academy of Sciences, 100190 Beijing, China
E-mail: gaoyan@mail.ioa.ac.cn