Dutch and U.S. researchers are testing new acoustics technology that could be mounted on the outside of small aircraft, listening for characteristic sounds that indicate the presence of other fliers. Called an acoustic vector sensor (AVS), the system uses nanoscale materials to alert pilots to other aircraft within about 10 kilometers, a system that may help prevent midair collisions such as the one between a private plane and a sightseeing helicopter over New York City's Hudson River in August 2009, the researchers say.
Radio transponders, used globally to track air traffic, are not required in small and private U.S. craft, a possible factor in the New York tragedy. And whereas some private pilots have installed transponders or newer GPS devices, those systems can only track other planes that carry similar equipment.
AVS, being developed by Netherlands-based Microflown Technologies, does not transmit radio signals, pulse energy (radar) or bounce sound (echolocation), says Hans-Elias de Bree, the technology's inventor. Instead, AVS listens for sounds, which are passed to a small personal computer. (Test rigs use a CompuLab fit-PC2—for analysis and display.)
So sophisticated is AVS, engineers say, that it can monitor multiple aircraft, picking up engine and other flight sounds and computing the vehicles' heading, speed and altitude. It can even tell if a propeller engine is straining under a heavy load by the "blade slap," or the sound of a propeller cutting through the air.
AVS anatomy
The heart of AVS is an anemometer—which measures wind speed—that can pick up sounds in a 360-degree sphere while moving through the chaotic air traveled by small planes. De Bree applied for an AVS patent in 1995 and co-founded Microflown to commercialize it.
At one millimeter wide, two millimeters long and 300 micrometers thick, the anemometer is smaller than a match head. It consists of two resistive platinum strips, each 200 nanometers thick by 10 micrometers wide, stretched parallel across a gap and heated to 200 degrees Celsius when operating.
Particles in the air flowing through the gap cause temperature variations in the strips that enable the sensor to do two things: First, it counts the air particles to measure sound intensity. Second, it records particle movement, which reveals the x, y and z coordinates of whatever made the sound. Researchers have measured its precision at less than 0.1 degree C within one kilometer.
Noise cancellation
Filtering software removes the ambient engine noise produced by the plane that is using the AVC. The data is read and analyzed by proprietary signal-processing software still being tweaked by Microflown.
Signal processing "is nontrivial," says Richard Lueptow, a mechanical engineering professor at Northwestern University in Evanston, Ill. "You can account for wind noise and aircraft noise and such, but it's tricky."
Tricky, but possible, says Lueptow, adding, "The idea is not unreasonable.
Grunge fighting
The sensor itself can be mounted flush on the aircraft's skin or protected in a bullet-shaped wind shield that protrudes from, for instance, a wing's leading edge. A collar made of solid nickel foam near the base of the wind shield allows air particles inside. One sensor can monitor all of the surrounding airspace, according to de Bree, because it is reading the motion of air particles, not the arrival of waves.
Being so tiny, the sensor could easily be overwhelmed by substances in the air, and at these scales anything sticking to the platinum strips degrades their effectiveness. So Ron Barrett, an aerospace engineering associate professor at the University of Kansas in Lawrence, is working closely with Microflown to protect the sensor from airborne grunge and water.
Tests are ongoing, but Barrett and his team in the school's aerospace engineering department are focusing on piezoelectric elements to induce infrasonic, sonic and ultrasonic vibrations in the strips. The vibrations atomize water droplets when they strike the strips and shake off solid particles, he says.
To date, a stationary AVS system has monitored flybys of a helicopter and a small plane, tracking the craft to within several feet, Barrett says. This spring, de Bree intends a dynamic test with a pair of helicopter drones, one tracking the other.
"There are no physics-based walls" preventing commercialization, Barrett says, "just technical challenges." AVS systems for aircraft should cost $10,000 each, based on shipping 1,000 units per month, he adds. Comparing the AVS price with GPS and transponder systems is not straightforward, because typically the latter systems are sold as part of new planes. They can, however, be purchased piece by piece, for prices that vary greatly, and installed by a service firm for a separate fee. A relatively simple aircraft GPS from a name-brand company like Garmin might run about $2,000, whereas more complex systems with multimode transponders, distance measurement and other functions cost about $12,000, without installation.
Remaining hurdles
Three nonengineering, nontrivial hurdles will need to be crossed before Microflown starts an assembly line: First is research money. With adequate funding, a finished product is "a year away," Barrett says, adding that it would be five to 10 years without the support.
Second, regulatory approval is anything but guaranteed. The Federal Aviation Administration (FAA) already is invested in automatic dependent surveillance–broadcast (ADS–B) and is cajoling private pilots to adopt the technology. ADS–B relies on proactive communication between GPS satellites and transponders placed on board aircraft to inform pilots, other aircraft and air traffic controllers about an aircraft's identity, location, speed and altitude. Barrett says he's had trouble engaging the FAA about AVS. (Although an FAA spokesperson initially said she would provide an FAA source to comment on AVS for this story, subsequent telephone calls and e-mails went unanswered.)
The third hurdle will be convincing private pilots, who pride themselves on self-reliance, to buy and install the system. A typical example is Dave Morrow, who co-owns Blue Skies Flying Services at Lake in the Hills Airport in northeastern Illinois. As a private pilot, Morrow says, "I don't want anymore stuff in my plane. I'm a strictly [a] map-on-my-lap kind of guy."
To that, Barrett says, fine. So long as pilots who want some more situational awareness can hear Morrow and other rugged individualists coming.
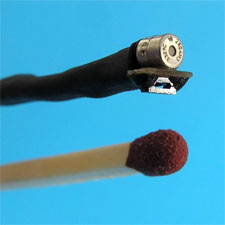
ACOUSTIC VECTOR SENSOR: AVS uses nanoscale materials to alert pilots to other aircraft within about 10 kilometers. The heart of AVS is a one-millimeter-wide, two-millimeter-long and 300-micrometer-thick anemometer (which measures wind speed) that is smaller than a match head but can pick up sounds in a 360-degree sphere while moving through the chaotic air traveled by small planes.
From: http://www.scientificamerican.com/article.cfm?id=acoustic-vector-sensing